Hello, I’m working on a project to make a custom sissy bar for my 86 Yamaha Radian that allows for a backrest, and no aftermarket sissy bars exist for the Radian besides some cheap Chinese generic ones, and It’s a little more rewarding to make my own.
I created a CAD model of about what I want (doesn’t always happen)
For rod is 3/4 diameter, and the 2 blocks to mount it will weld and are 3/8th thick
I don’t know how to weld, and I’m not sure how hard it is to bend steel of that caliber.
I’m pretty sure my brother or dad could weld, and cnc the blocks, but the curved steel seems like a big roadblock.
If anyone has advice or has bent steel like this, please let me know. Thank you.
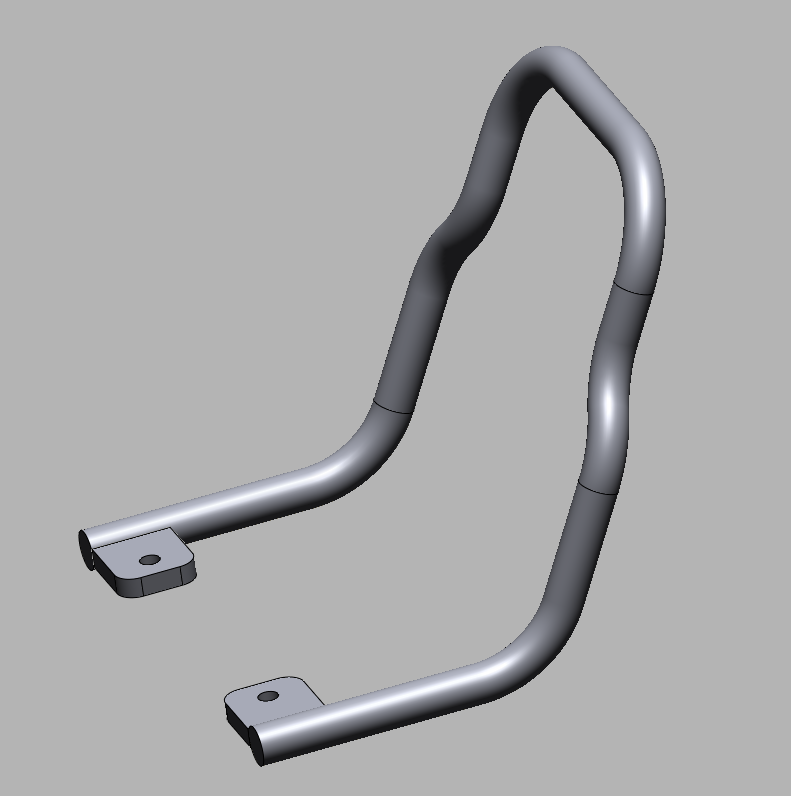
And heres a kind of shoop on the bike itself. I plan on making a leather cushion as well. (which I know a lot more of)
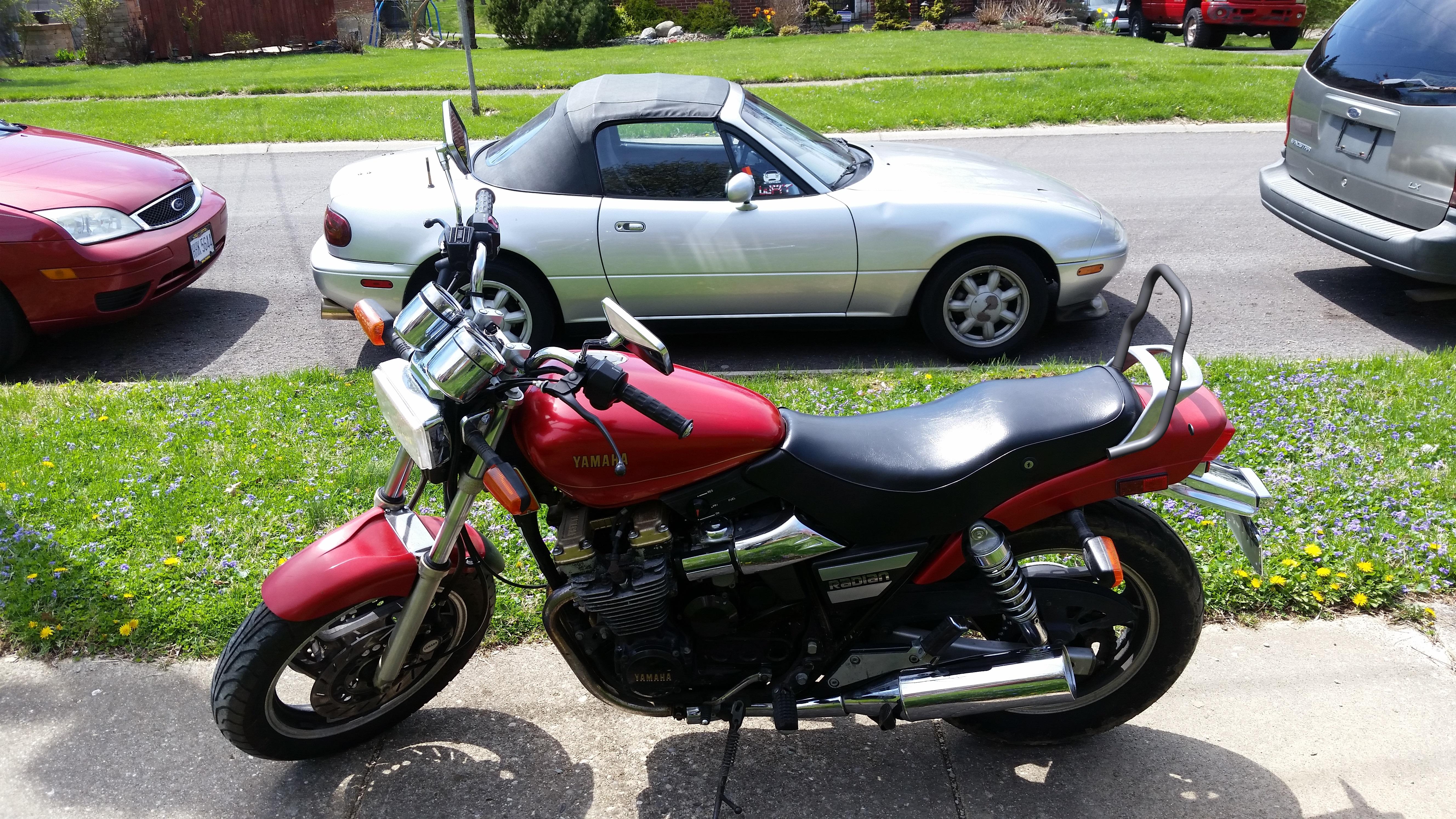
Will just brought in a block bender for Hive13 to use, it should handle this no problem. 3/4" solid is pretty stout, but should be manageable, even if heat is required. Tube may be easier though.
those end blocks are simple enough you shouldn’t need CNC, our manual mill would do it just fine.
do you want plain steel or stainless?
Kevin,
Thats great! I was looking on the Wiki for tools and couldn’t find anything bending wise, but is great we have something. I read online that you’d want to only heat it to red. Anything past red will ruin the shape.
as for the blocks, Yeah, I figured, it’s a block with a hole, and 2 fillets.
Finally, the steel type, Not sure, as I’d like to send it to get chrome powder coated to keep with the design of the bike, So whatever goes best with a powder coat.
Thanks for your help.
If you want it powdered, there is no reason to deal with the headaches of stainless.
Tube would be significantly easier to bend, but if you want solid we can certainly make that work. might be able to use the glass torch to heat the sections, though it’d be easier if you bought a few bottles of MAPP gas and used hand torches.
I don’t mind helping you through the process. The mill and welders are certification required tools, Ideally you should get certified before doing this project (we can probably work out times to do certification to help you out). I can walk you through certification on the MIG welder, if you want TIG you will need to ask around, not sure who can cert on it right now. As for the mill, I think Dave V. and Brad both have done Mill certification classes?
If you just want to get this specific project done before full certification, I’m sure we can help you out.
Kevin,
Im looking around at tubing, It might not be a bad idea, It’s definitely easier to work with. I’m not sure it would bend or break with alot of pressure that someone leaning on it could cause. I just looked at some 3/4 inch tube we have in our shop, and I might want to take it down a size, now that I’m looking at it, maybe 1/2 would do a lot better. I also measured my CAD with the OD being .75, not the ID. I’ll head out and get a 1/2 tube if It seems like what I want. I honestly feel like I wouldn’t use the metal area a lot until I’ve taken my manufacturing class at Cinci state, as I don’t have a real use for it besides the bar.
Thanks
If you are going to school at Cincinnati State, ya might want to swing past the aviation building and welding shop. When I was in the aviation program they had nice tube in mild / chromoly / and some stainless that we used for engine stands and our own powersports stuff. They may have some scrap you can play around with. Mild and chromoly are great for powder coating and weld up fairly easy. From looking at your shapes, you might be able to buy a diy performance header kit from jegs or summit that will help with having perfect cnc bends and the stitch it all together. You could rapid prototype for really cheap going that route.